THE H2020 PROJECT DRIVE 0 HAS BEEN KICKED-OFF, LOOKING FOR CIRCULARITY IN BUILDINGS.
How can a circular building be defined? And what about a circular renovation process?
These are the main questions the researchers, architects, engineers and other partners of the H2020 Drive 0 project asked themselves during their first meeting in Maastricht. I was glad to be part of them, representing Pich Architects together with Felipe (Pich Aguilera, the founder of the studio). Since 30 years the studio has been advocating sustainability and industrialization in architecture, and since the circular economy is becoming part of the construction sector, we underline that it represents the principles we believe in.
So how can circularity be defined, and more importantly, applied in the construction? Not to get lost in theory, lets start with some concrete proposals. There are 5 industrial partners in the Drive 0 project, each of them proposing a different point of view to circularity.
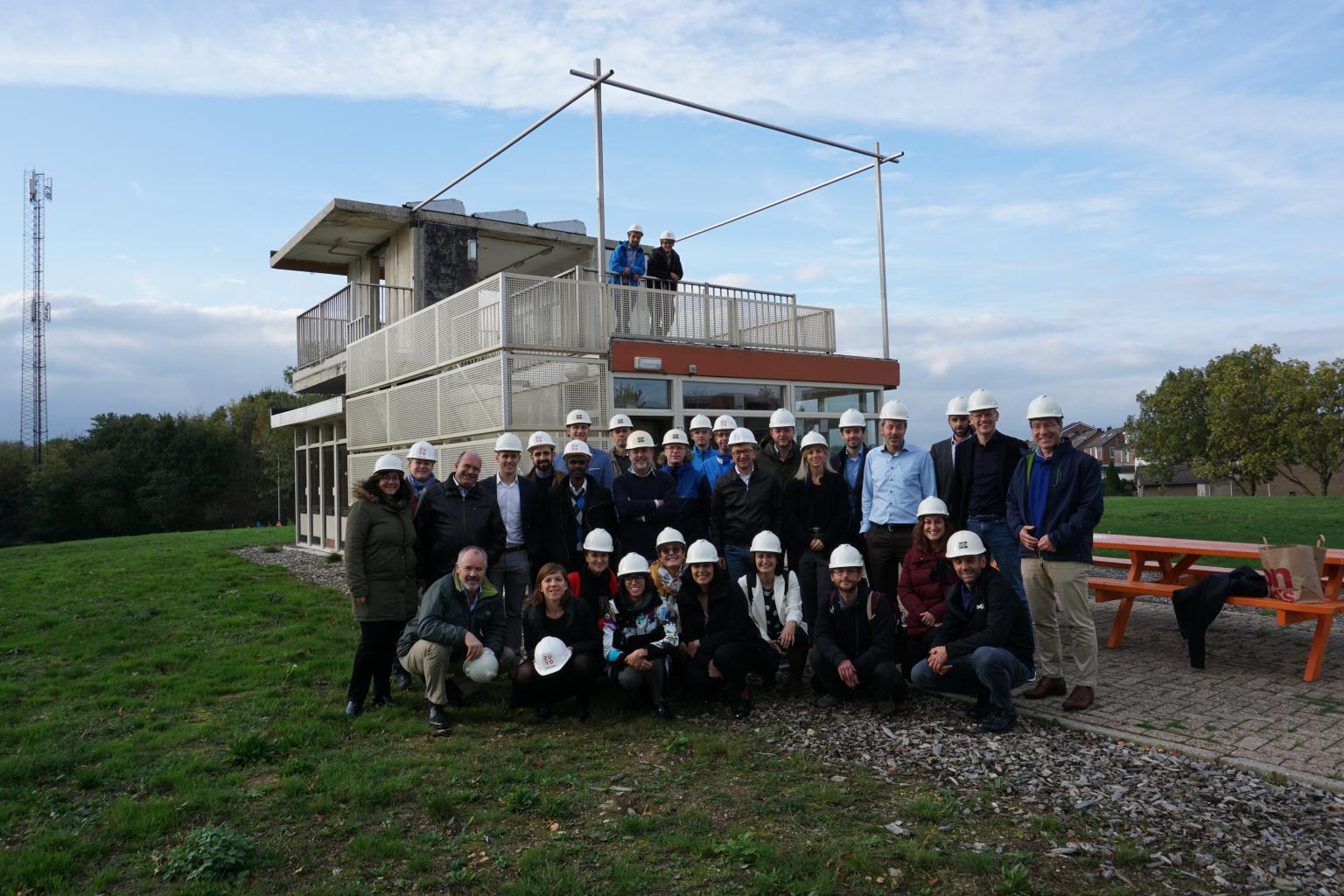
Drive 0 consortium at the Superlocal Site visit during the kick-off meeting 10/2019
WEBO from Netherlands, manufacturer of windows and prefabricated facades proposes a window without frame, window with frame made of recovered wood, or window with frame with detachable aluminium part. The strategies here are to eliminate unnecessary materials, reuse and design for reuse and recycling, respectively. Which one of them is the most cirular? Does it depend on circumstances?
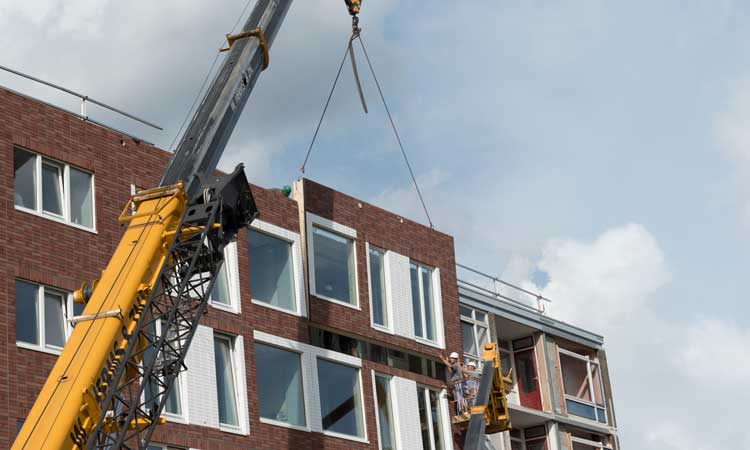
WEBO Scaffold Free Facade
TIMBECO, a company based in Estonia also produces wood based facade panels. Their approach to circularity includes making the facade panel cheaper, while keeping the high quality, so more people can afford it and decrease the heat losses by the envelope and so save energy. The company also considers application of recycled materials, which would decrease the environmental impact of the product. Not to forget they already use wood as the main material for the facade panel, having a more positive effect on the carbon footprint.
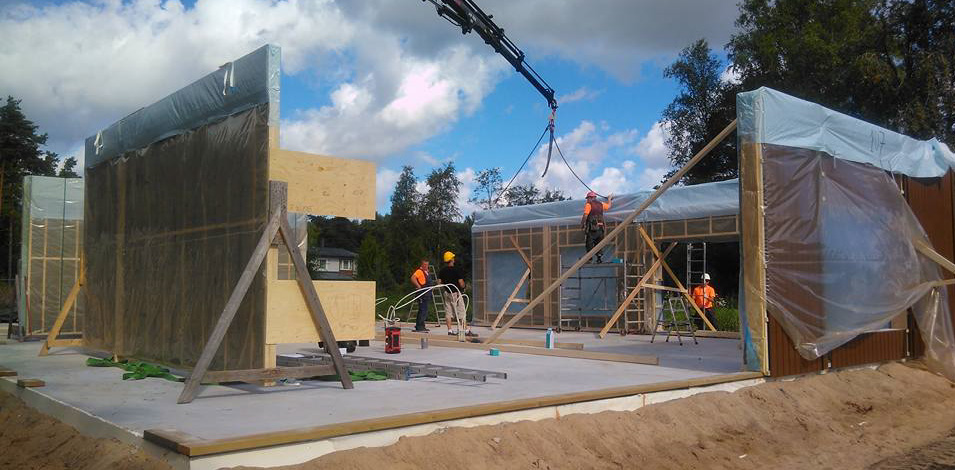
TIMBECO prefab construction
Factory 0 is another industrial parter from Netherlands, in their case providing an integrated HVAC system for retrofit, a good-looking kit that includes all the necessary equipment to creat comfort in the renovated building. Their philosophy is to decrease the price of the energy efficient installation to allow more people to afford to retrofit their home, and so to decrease their and the overall energy consumption. That definitelly helps to decarbonize the building stock. Furthermore, they work on the elimination of unnecessary components of the individual machines too, integrating them together.
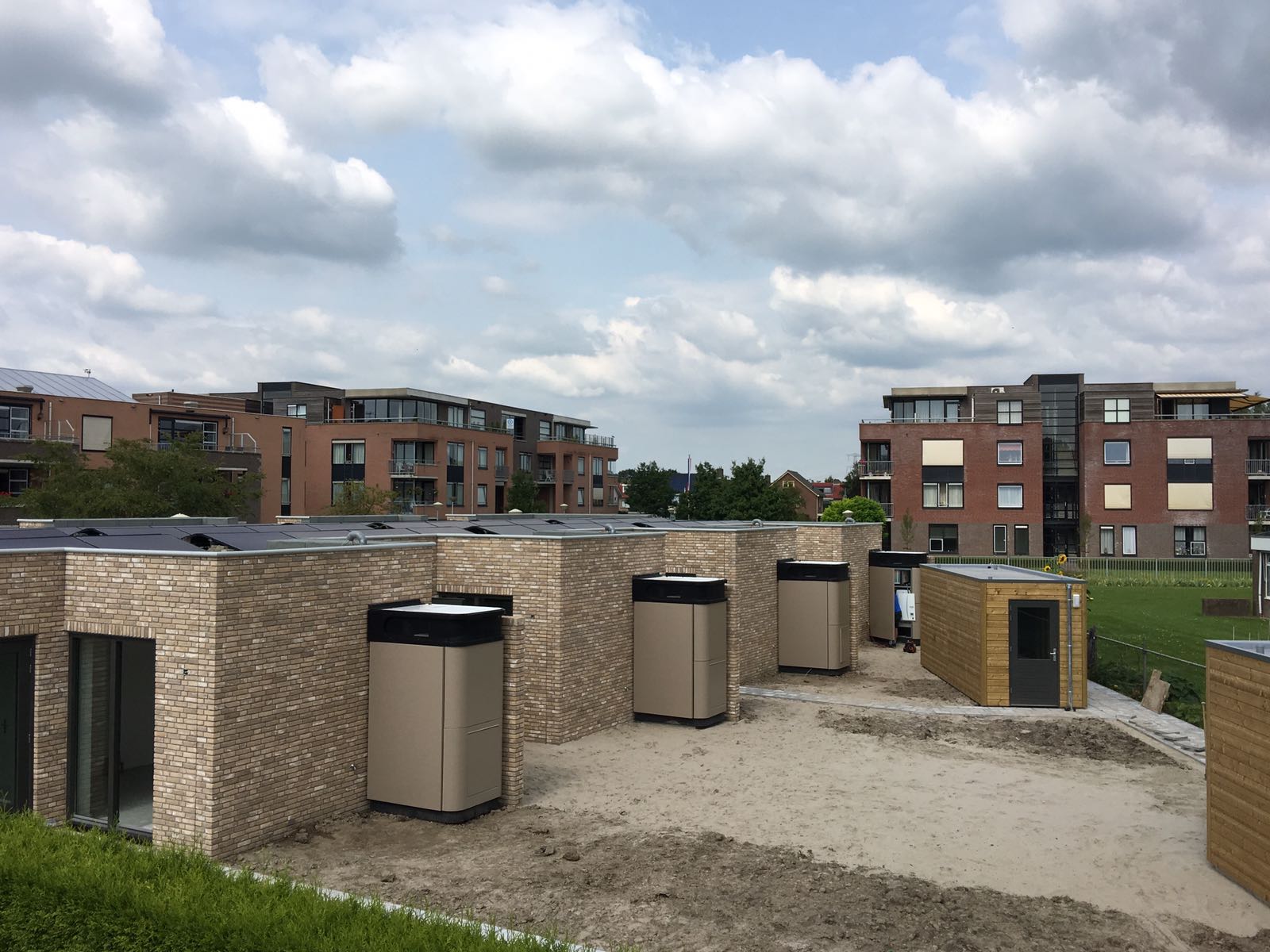
Factory Zero compact installation kits
ALIVA from Italy is a facade solution provider. They provide several sustainable measures, such as 100% aluminum cladding, reusable and recyclable, PCM based soutions for higher energy efficiency, or 3D sceleton in aluminum with plug-n-play nodes for light construction. Aluminum is a material that well represent the technical cycle of the circular economy (butterfly diagram). Although the embedded energy of a new aluminum component is quite high, it is very durable and can be easily reused, as well as recycled in case it it not a composite material.
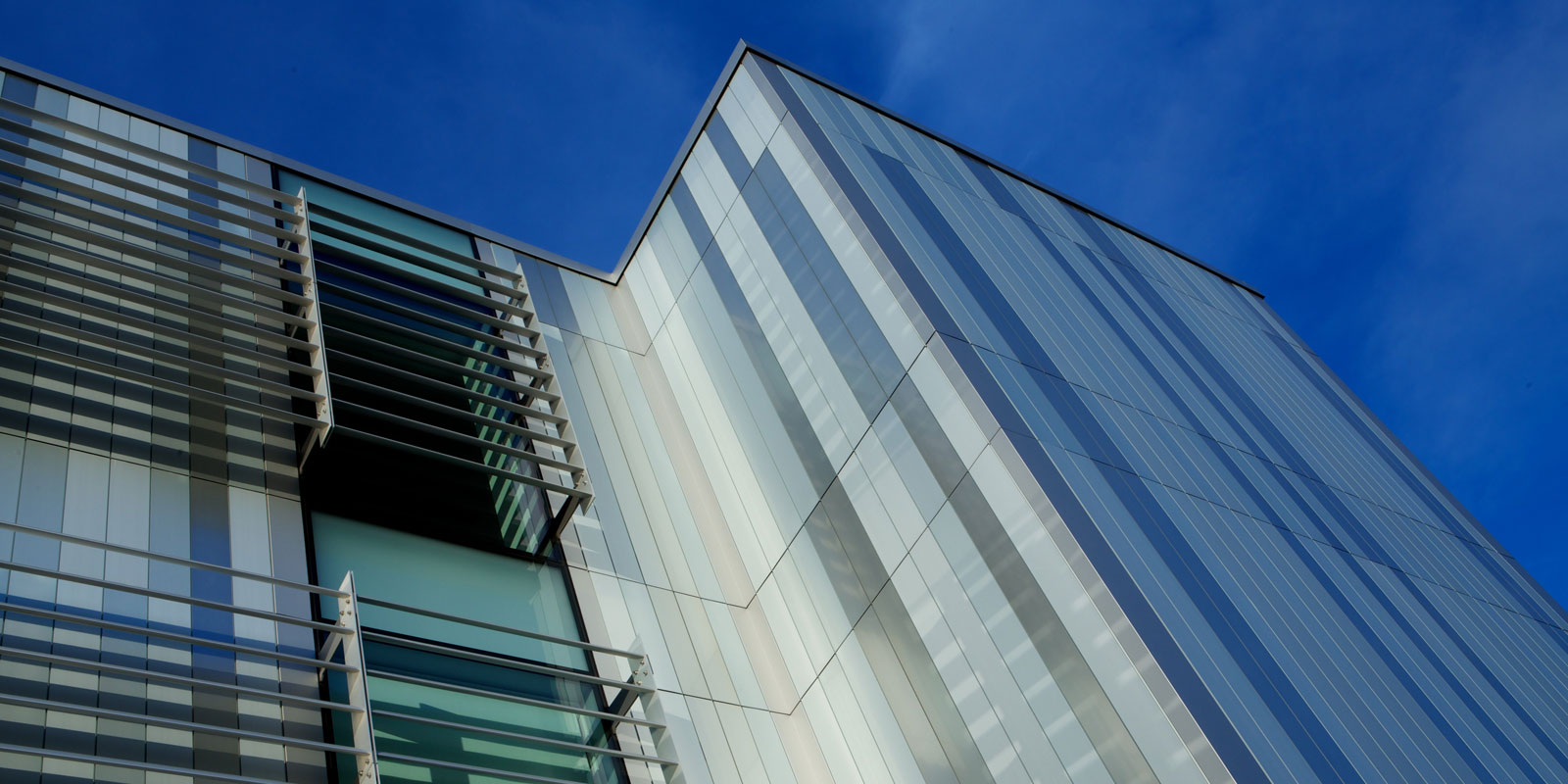
ALIVA Alcovering facade
KNAUF INSULATION Slovenia comes up with another different approach. They manufacture glass wool and rock mineral wool with a bio-based binder, so they manage to avoid use of formaldehyde, as well as have extremely low VOC (volatile organic compounds). Apart of decreasing environmental impact of the product, there is an important positive impact to the health. In Slovenia they also reach up to 80% recycled content in the glass wool, and up to 45% of recycled content for their rock mineral wool, by reclaiming their products from the construction sites and production lines.
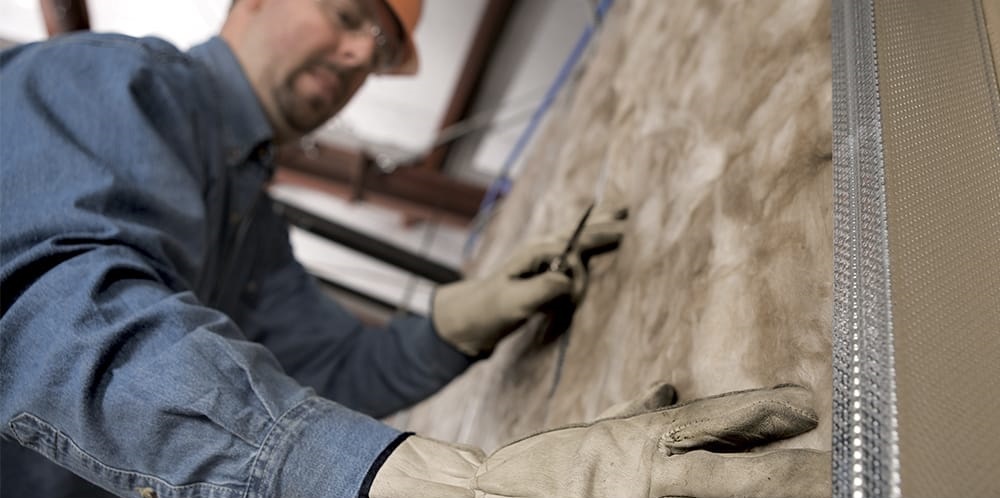
KNAUF Insulation
Are all these measures sustainable? Circular? Circular enough? Probably there is no absolute answer. There is maybe even a better, more circular solution. But they are definitelly a big step ahead compared to the current practices.
These were examples of what an industry can do. How about architects and property owners or investors? Well, in Maastricht and surrounding we have seen 2 amazing examples.
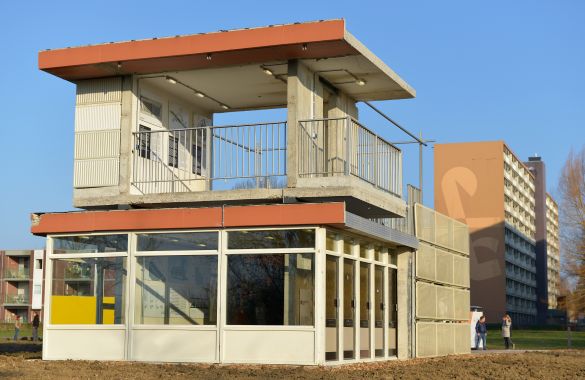
Superlocal project Kerkrade, picture by duurzamescheurkalender, check also: https://www.superlocal.eu/
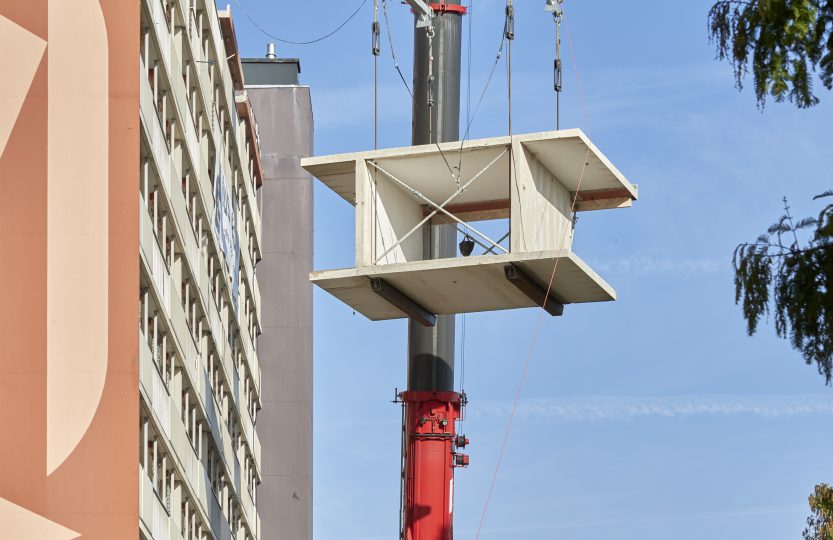
Superlocal project Kerkrade, picture by bouwbedrijvenjongen
One of them, presented by one of the Drive 0 partners ZUYD. There is a large building stock to be demolished in the region, because of decrease of its population. But what if the buildings do not have to be demolished? Or, at least not entirely? The Superlocal project explored the possibilities to reuse the existing construction, at the components level, and at the material level. There is a pilot building reusing the structure of one former apartment and many other components, like doors, carpentries or railings. Another experiment involves recovering the concrete in form of aggregate, desintegrated directly on the construction site from the concrete components, to form new concrete to construct new individual houses on the same site.
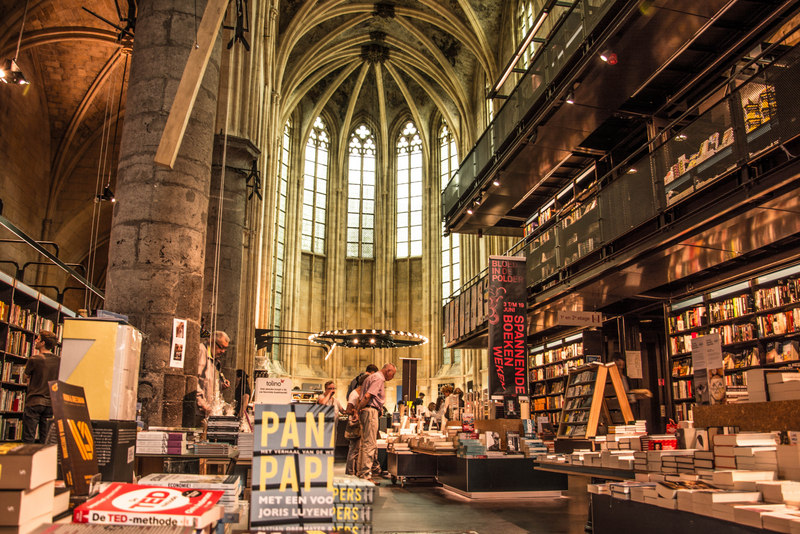
Boekhandel Dominicanenin, bookstore in Maastrich, photo by tripsandbooks
Another example can be found in the center of Maastricht. Can you imagine a bookstore in a church? Or even a hotel? The Kruisherenhotel is composed of a former Gothic church, which now houses the reception area and several hotel facilities, including conference rooms, a library, a boutique, a restaurant, and a wine bar, and of a monastery converted to 60 hotel rooms. The architectural firm SATIJNplus Architecten managed to place all the functions needed to the existing space, almost without touching the original construction.
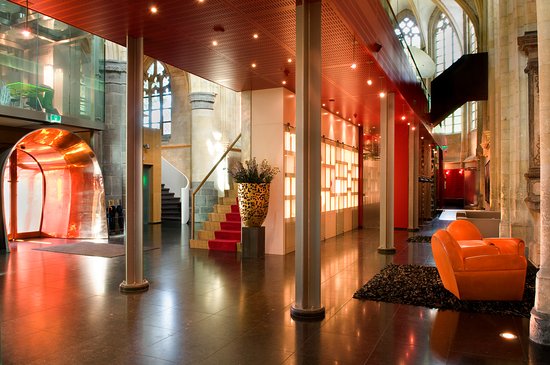
Kruisherenhotel Maastricht lobby, picture by Tripadvisor
This last example is in terms of environmental impact the best to be done. Instead of building a new building, an existing and unused building is converted for a new use.
The only even better option is doing nothing. Nothing costs no energy, and no material is used. What does it mean for the construction sector in practice? To keep in use what we have as long as possible, to maintain, repair, take care of the buildings. This where it comes to the users and their role in the circular economy. The users are crucial to extend the life of the buildings and their components, to allow to explore the full potential given by the durability of the building materials.
This may seem as a conclusion, but in a circular economy, not even a conclusion can be linear. Doing nothing saves materials, but does it necesarrily save energy? The total energy used by a building is mainly due to the energy embedded in its materials, and the energy used to keep the comfort in the use phase. If a retrofit manages to save more energy, than it is embedded in the materials and technologies needed for the renovation, it makes sense. Concepts like using resused or recycled materials keep the embedded energy low, while passive design strategies such as insulation, shading or thermal inertia, as well as efficient technologies decrease the operational energy.
We should use as little material as possible to allow the buildings to use as little energy as possible. As close to 0 as possible. A circular 0.
This project has received funding from the European Union’s Horizon 2020 research and innovation programme under grant agreement No. 841850.
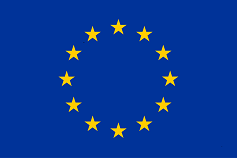